- HOME
- Business
- Industrial Robot
Industrial Robot
We apply industrial robots to high-risk, high-intensity sites to make your industrial sites safe and more productive. We provide robot automation services ranging from consulting, design, construction, and to operation for robot applications centered on software technology.
Robotic Automation Specialist
- Design, build, and operate robotic automation systems tailored to customer needs through collaborations with robot manufacturers and process 3D design and simulation.
- Expertise in control system and facility automation with experience in automating manufacturing plants and building smart factories.
- Differentiated technology, such as a robot control platform. ACS: SW platform that can control heterogeneous logistics transfer robots.
-
Factory Automation
(1980-) -
Smart Factory
(Smartization, 2016-) -
Robotic Automation (unmanned, 2022-)
Robotic Automation Based on Standard Models and Methodologies
Standard Process Model
'Process-specific' standard model with robots → Faster expansion of the same process.
※ Automated 4-continuous casting based on STS steelmaking automation model
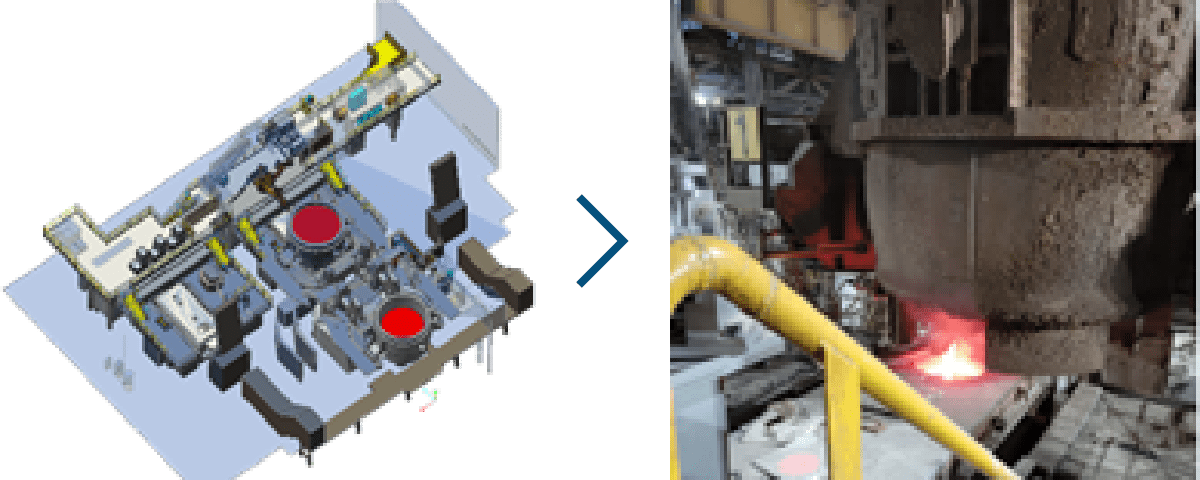
Standard Functional Model
"Function-specific" standard models of robotic tasks → Reusable in new robotics automation projects.
※ Reusing the molten steel sampling function in the blast furnace outlet molten iron sampling.
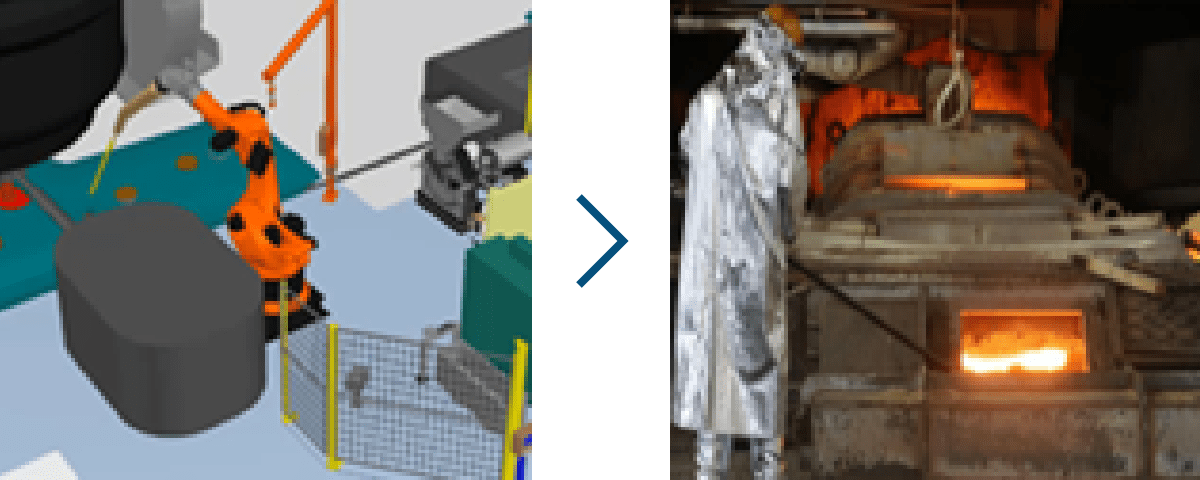
Service Model
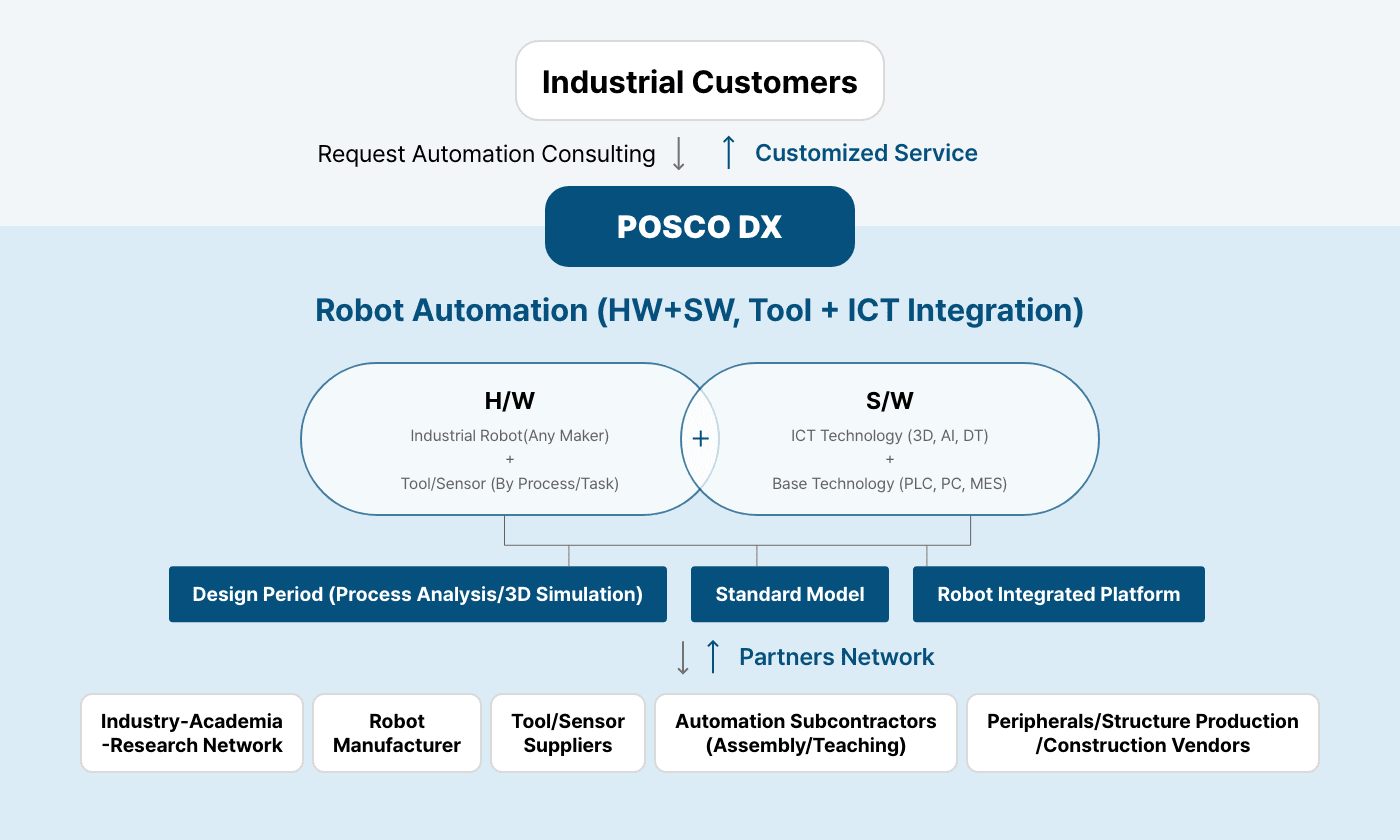
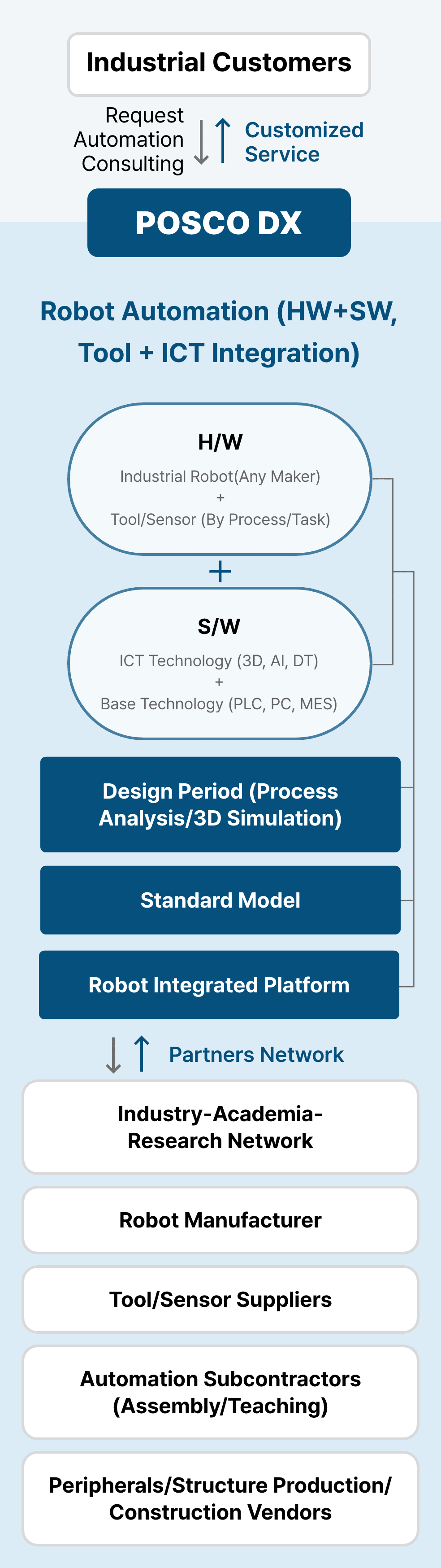
Service Areas
Manufacturing Robotic Automation
Creating safe work environments in high-risk, high-intensity industries and increasing productivity in manufacturing processes.
Building a standard model for robots in high-risk tasks
- Robotic automation design based on 3D design, simulation, and OLP.
- Analyze issues of current processes, identify improvements, design automation and minimize field work.
※ Ladle Man Deck robot automation, plating dross removal, band cutter automation, etc.
Increasing productivity for midsize manufacturers with smart factory business
Proposing proven robotic automation systems to existing smart factory customers.
Logistics Robot Automation
Automation of movement between warehouse and process in the manufacturing process of receiving → production/manufacturing → shipping

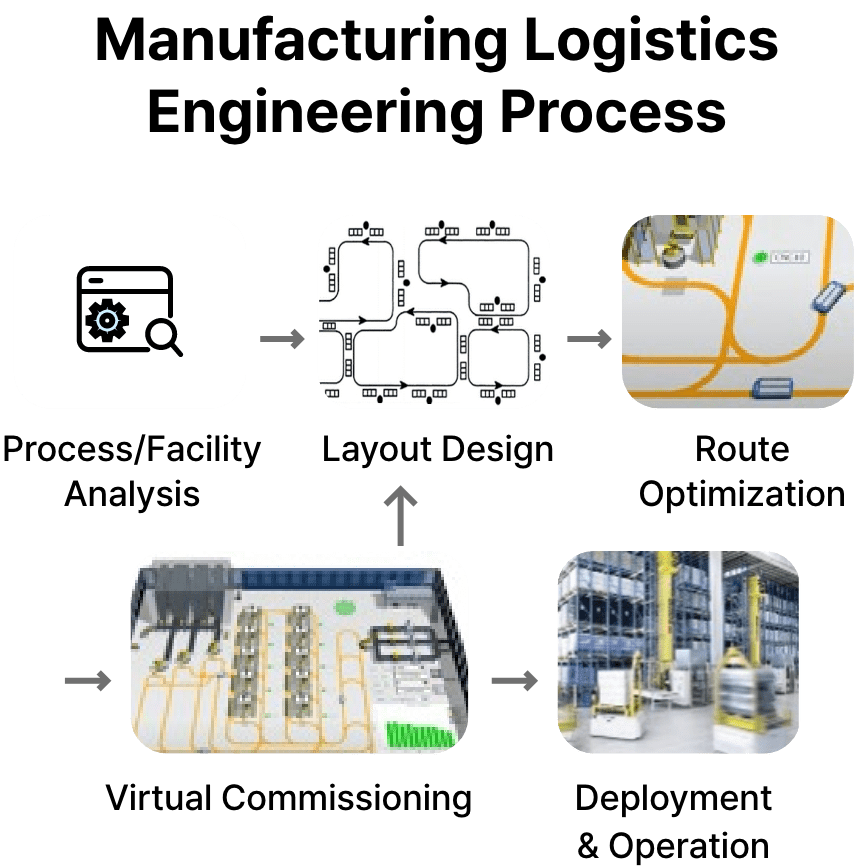
Manufacturing logistics design based on the process of analysis → design/optimization → virtual commissioning
Rationalization of POSCO Future M's non-calcination plants and calcination plants.
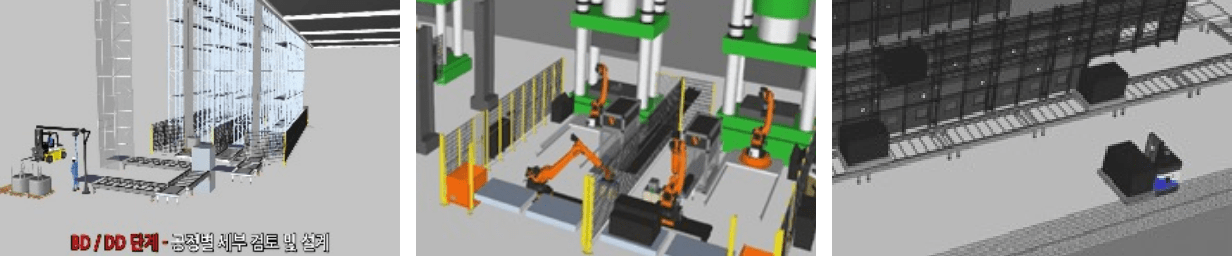
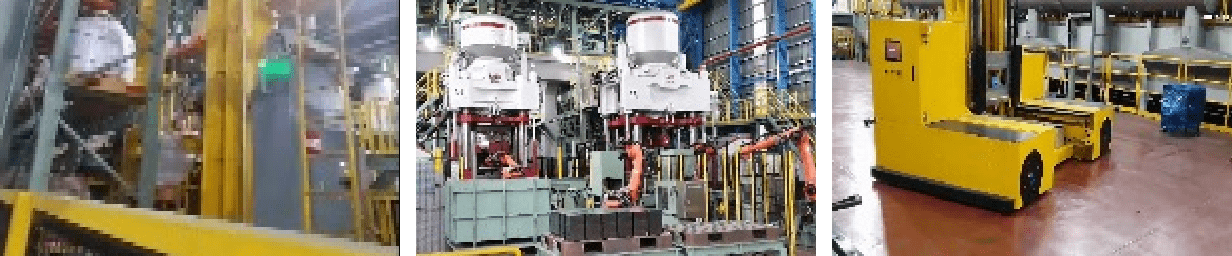
Heterogeneous AGV/AMR integrated control system (ACS)
- Operation and monitoring of heterogeneous AGVs centered on ACS (AGV Control System)
- Standardization of introduction/operation through ACS application
※ POSCO Future M cathode materials, PFC, etc.
Differentiators
Designing robotic systems based on engineering skills
Differentiating design with 3D engineering technology
- Analyzing issues in the as-is process and generating improvement ideas to design the to-be concept
- Reducing project execution costs (trial and error) with 3D simulation validation
- Validating investment feasibility (facility utilization, workforce reduction, etc.) and proposing systems
- Assetizing technology and reusing it in other projects
-
STEP 1 As-is Process Analysis
-
STEP 2 3D Capture of Real Environment
-
STEP 3 To-be Concept Design
-
STEP 4 Simulation OLP
-
STEP 5 Commissioning & Feasibility
ACS driven optimal operation of AGV/AMR
Data-driven formation control and optimized operation techniques
- Standardizing interface and configuration as the steel mills and group companies expand AGV applications
- Recognizing real-time vehicle congestion while driving to enable dynamic rerouting
- Achieving the shortest travel time, not just distance
- Recommending optimal AGV spec/number through preliminary analysis of volume, utilization, etc.
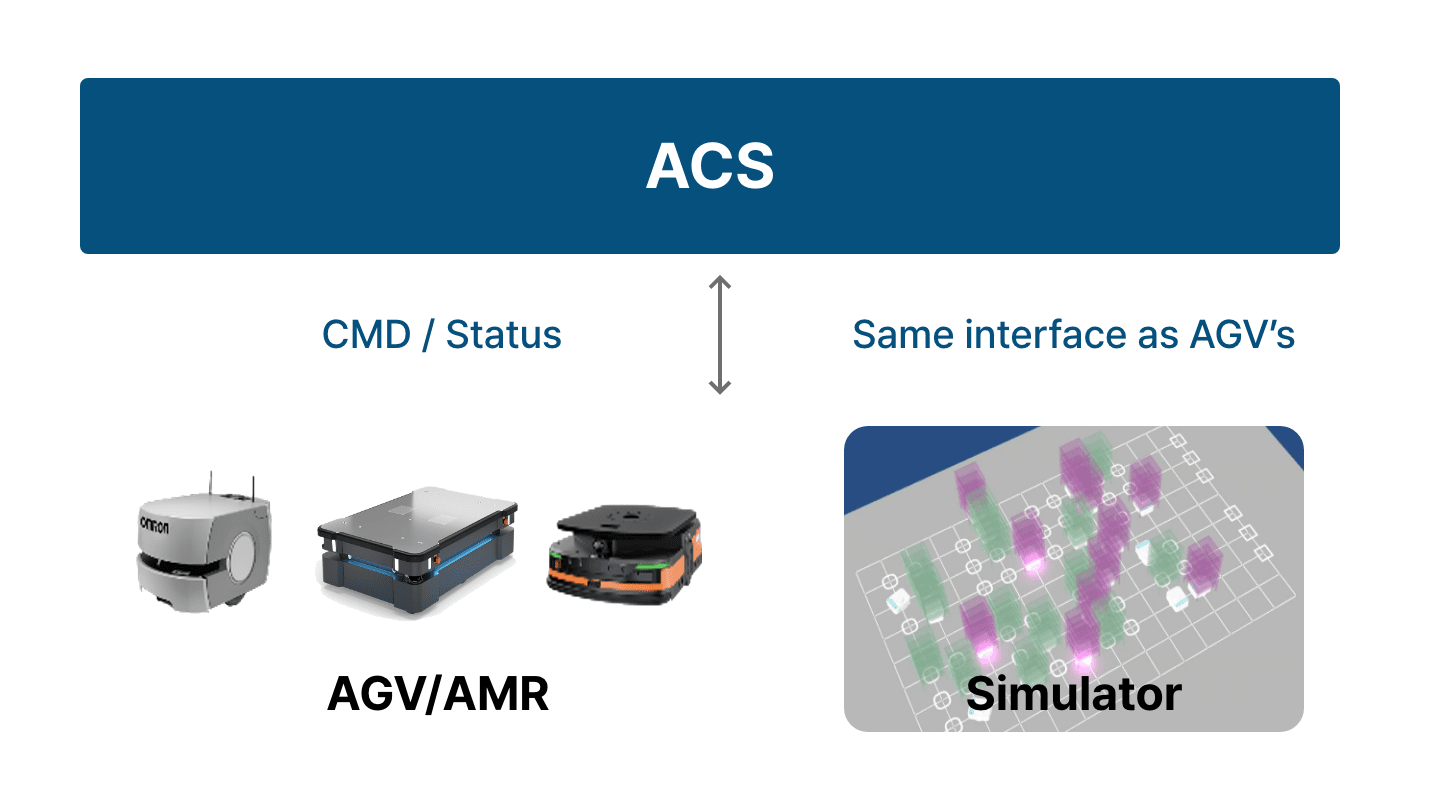
- Designing middleware to work with upstream and downstream systems
- AI-powered optimal logistics scheduling
Categorizing suppliers by brand/characteristic/size and establishing a cooperation system
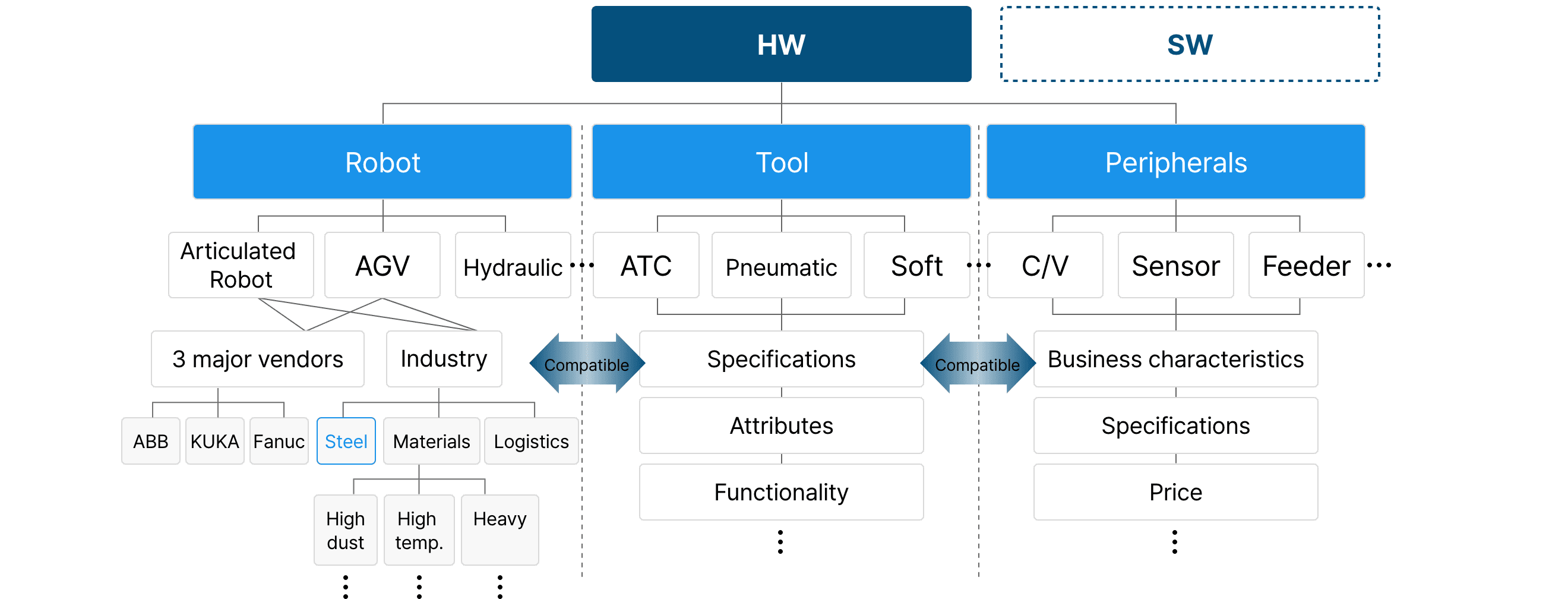
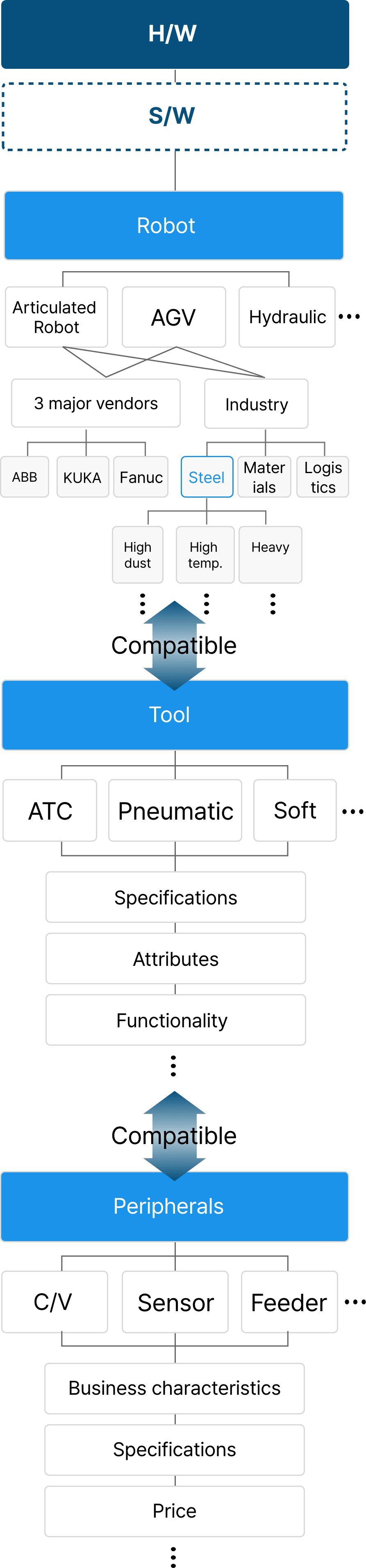
Key Achievements
-
Manufacturing robot
- Automation of cold rolled coil band cutter at POSCO Pohang Steel Mill (Automating the removal work of bands attached to coils)
- Deployed galvanized pot dross removal robots at POSCO Gwangyang Steel Mill (Automation of high temperature(460℃) zinc plating pot floating material removal process)
- Deployed stage-2 kiln saggar replacement robot at POSCO FutureM Gwangyang cathode material plant
(Automation of refractory vessel replacement in a cathode sintering furnace)
-
Logistics robot
- Deployed HyperNO electrical steel coil AGV at POSCO Gwangyang Steel Mill (Application of 65-ton AGV for Hyper NO electrical steel sheet transport automation)
- Deployed AGV at POSCO Gwangyang Steel Mill PFC (POSCO Fulfilment Center) (Material Transfer automation for Building a Central Warehouse Smart Fulfilment)
- Deployed stage-1/ stage-2 AGV at POSCO FutureM Pohang cathode material plant (Automation of raw material transport using AGV due to expansion of cathode material production capacity)
- POSCO FutureM Gwangyang cathode material plant 5-stage AGV
- UltiumCam Quebec cathode material plant AGV