- HOME
- Business
- Smart Factory
Smart Factory
Data in the production site is collected in real time to be analyzed through Big Data, and optimum control is supported through AI. Through this, productivity improvement in the manufacturing industry is enabled along with quality competitive enhancement, while the management standards of facility, energy, and safety are improved to upgrade manufacturing competitiveness.
Smart Technology
-
Sensing(IoT, Connected)
- Things connected to the network through loT technology
-
- Data exchange between all entities in the world such as people and things, etc.
- Exceeding the connection of simple information to provide infrastructure for data convergence.
-
Analyze(Data-Driven)
- Analysis and prediction of future events based on Big Data
-
- Hidden patterns are discovered through diverse data to create new value.
- Linkage analysis of overall processes to discover invisible waste factors.
-
AI Control(Intelligence, Optimal)
- All system operations are optimized through Al for automatic control
-
- Failure is predicted without human intervention, and an optimum operating method is established.
- System/Facility state is predicted to optimally control the system.
-
Autonomous(3D Simulation, Interface)
- Real-time simulation and optimized autonomous operation in digital twin factory
-
- Predicts design, production, quality, and logistics results with real-time simulation in a virtual space identical to the field.
Evolution Strategy
Automate individual processes/equipment and make them smarter to optimize operations
Optimize individual factories and expand to value chain
Create a net of autonomous, flexible factories with a hyper-connected supply chain across the company
Strategies to Drive Smart Factory
-
- 01.Optimize for integrated process and inter-process penetration
-
Implement integration/penetration efforts for each department
-
- 02.Expand smart MES value chain
-
Smartize across business areas and customers
-
- 03.Expand digital twin from value chain to supply chain
-
Connect collaborative ecosystems, including external supply chains
Service Area
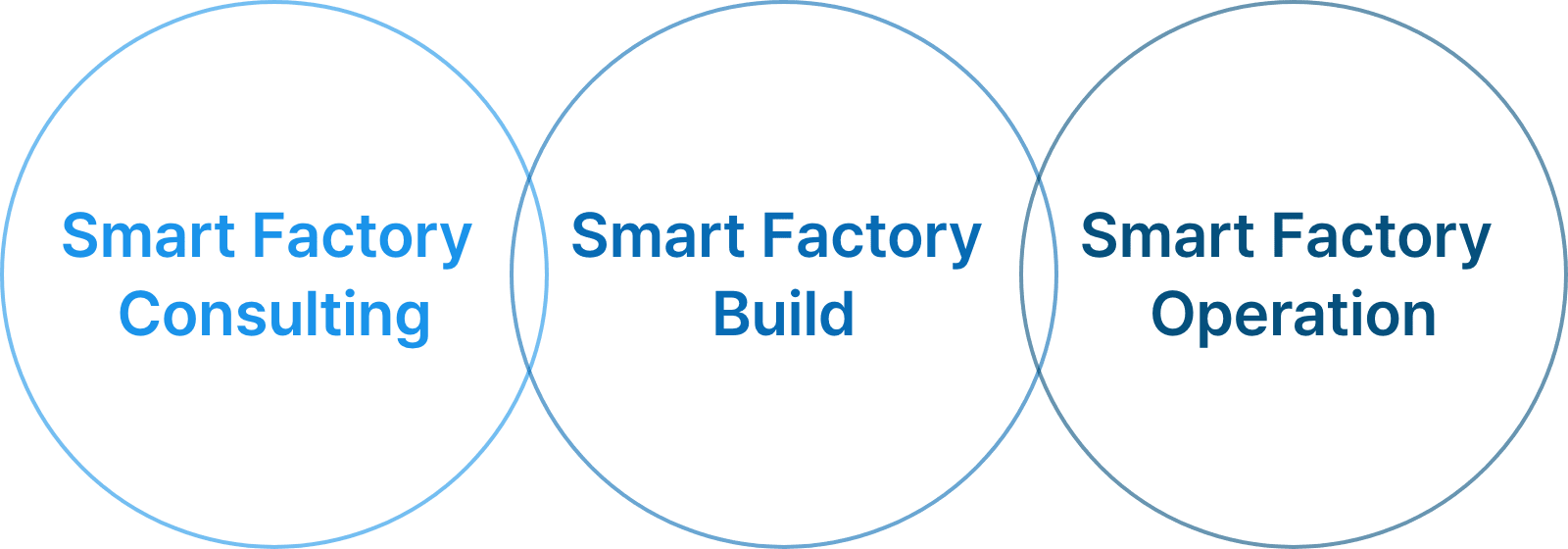
- Collaboration between DX and domain experts
- Production, quality, facilities, process logistics, ESG
- Establish strategies in all areas from diagnosis to success
- Control system with edge computing
- Leverage AI automated controls
- Secure and standardize data collection system
- Perform the entire AI modeling process
Smart Factory Consulting
After systematically diagnosing the level of the site, we establish a master plan that aligns the management strategy with the direction of the Smart Factory and provides the ideal direction.
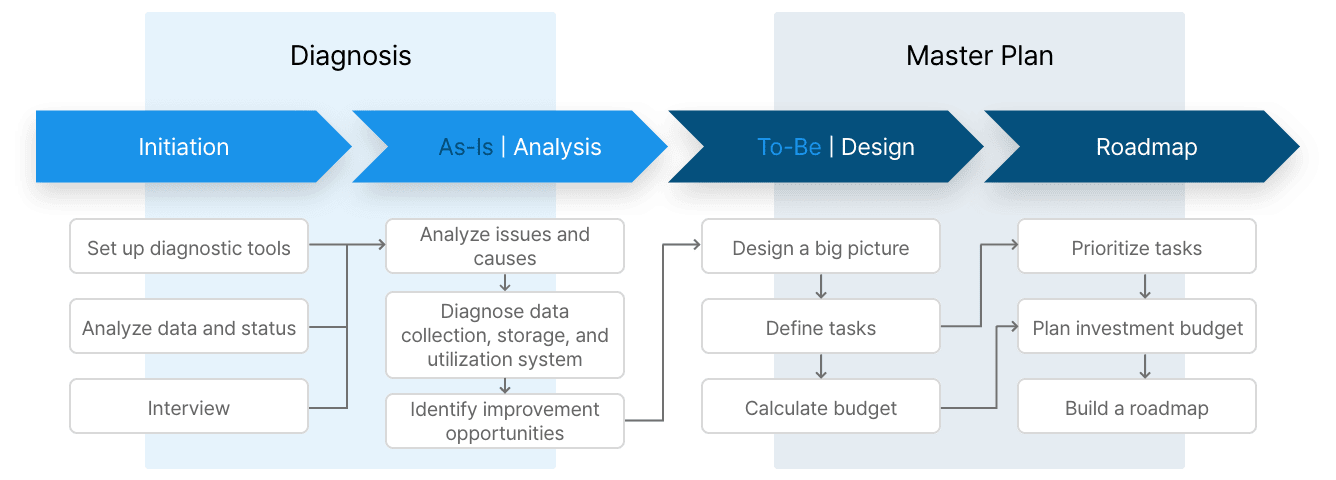
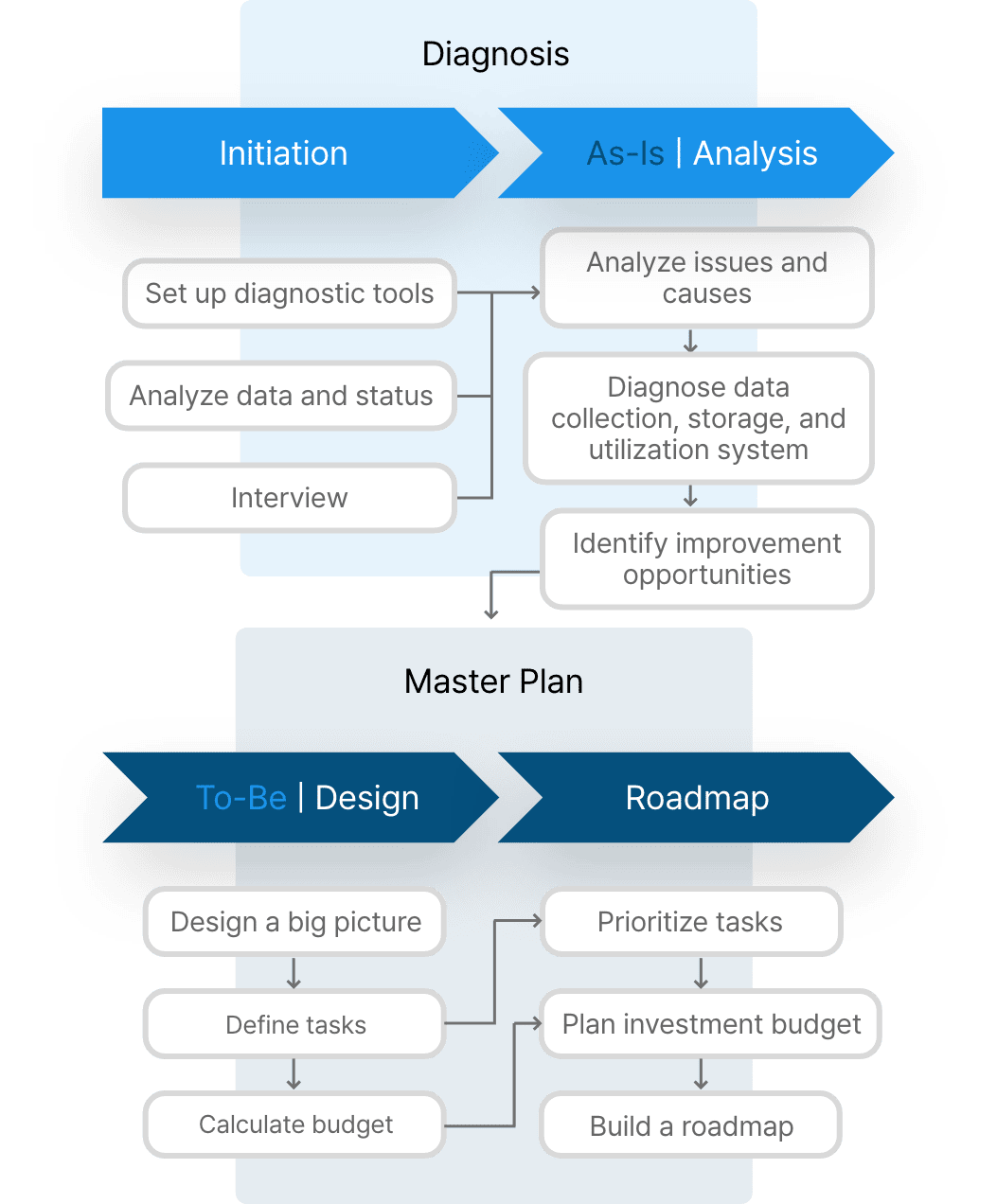
Smart Factory Build
We build a system for acquiring and utilizing data to enable data-driven decisions and operations.
-
STEP 1
Data Defining -
STEP 2
Data Standardizing -
STEP 3
Collection Automation -
STEP 4
Integrated Structuring
- Apply a high-efficiency, low-cost data platform and implement real-time data collection, analysis, and control
- Minimize the number of items by focusing on the most useful data
- Employ easy UI/UX for field engineers
We build systems that enable working engineers to perform the entire process of AI modeling.
-
STEP 1
Data Preparation -
STEP 2
Data Pre-processing -
STEP 3
Data Visualization -
STEP 4
Exploratory Analysis -
STEP 5
AI Modeling (Algorithm)
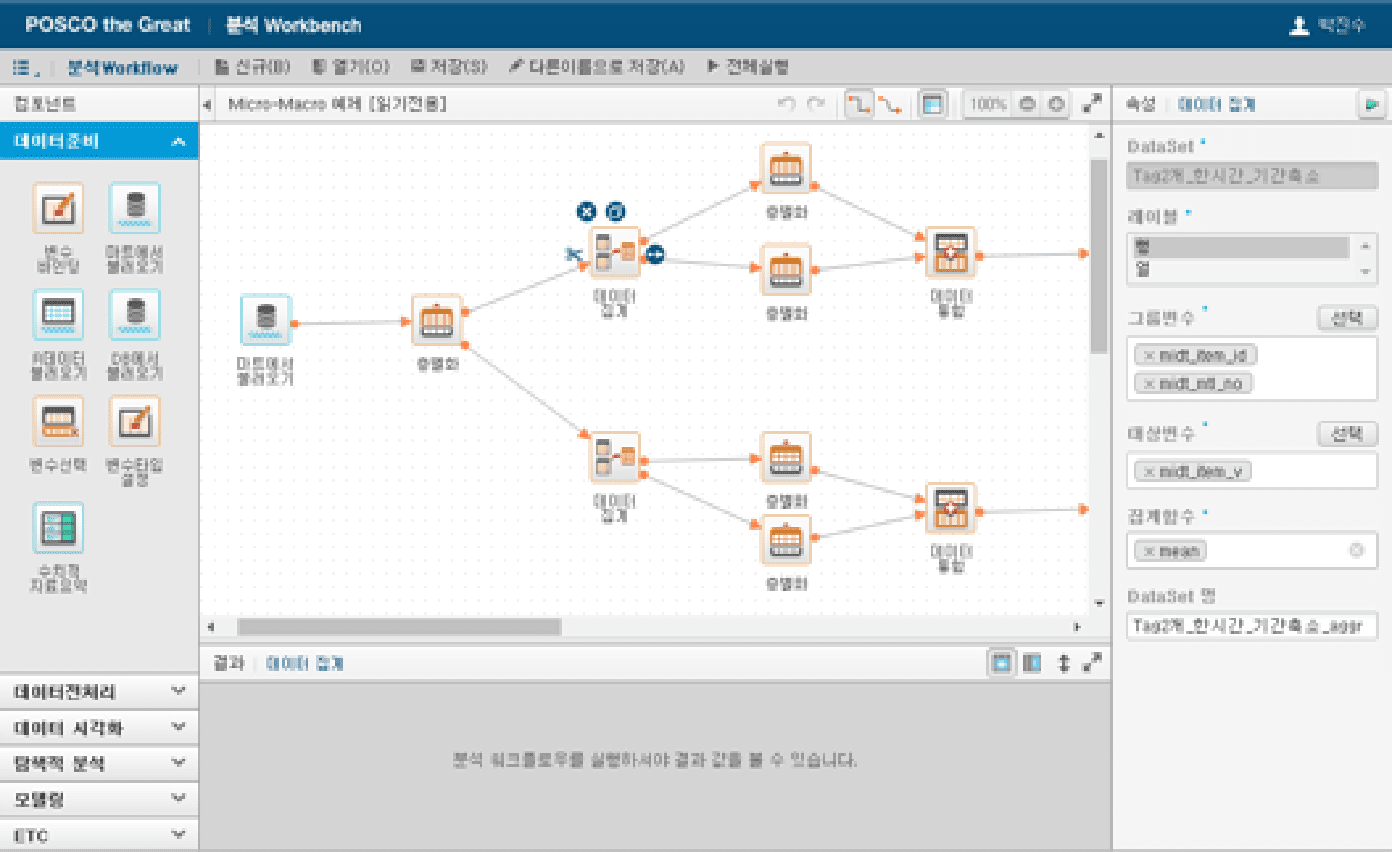
- Provide tools for non-analysts to analyze data and implement AI on their own
- Perform AI modeling with a menu that visualizes the entire analysis process
Smart Factory Operation
We use a deep learning-based control algorithm to provide operation guidance and switch to automatic control when the results are reliable.
-
AI Control Algorithm
Implement AI that learns from field know-how through deep learning
-
Operation Guidance
Verify the reliability of control results
-
AI Automated Control
- Build real-time control with edge computing
- Predict future conditions and take preemptive action
Digital Twin
A digital twin is a convergence technology that creates an exact 3D model of a real-world object in a virtual space and connects it to the real world, simulating what might happen to support optimal decision-making.
- Digital transformation of the entire factory with product/service visibility
- Leveraging field/simulation data to streamline product design
- Optimizing factory processes with simulation
- Real-time monitoring and emergency response simulation
- Improving maintenance efficiency by providing predictive information
Vision
Implement digital twin to simulate the entire process and support optimal decision-making.
Key References
- Smart Factory for POSCO Pohang/Gwangyang Works
- Smart Factory for LS MnM (Formerly, LS-Nikko Copper) Onsan Site
- Smart Factory for Pungsan Ulsan Site
- Smart Factory for DAESUN Distilling Busan Site
- Smart Factory for Hyosung Heavy Industries
- Smart logistics system for Kukdo Chemical