- HOME
- Solution
- Logistics Automation
Logistics Automation
POSCO DX aims to be a total logistics solution provider that provides everything from automation equipment for smart logistics centers to logistics solutions.
Logistics Automation System
To be flexible in responding to customer requirements and to apply the optimal solution to the customer site, we provide smart automation systems to a whole range of logistics processes and levels.
Logistics automation technology framework
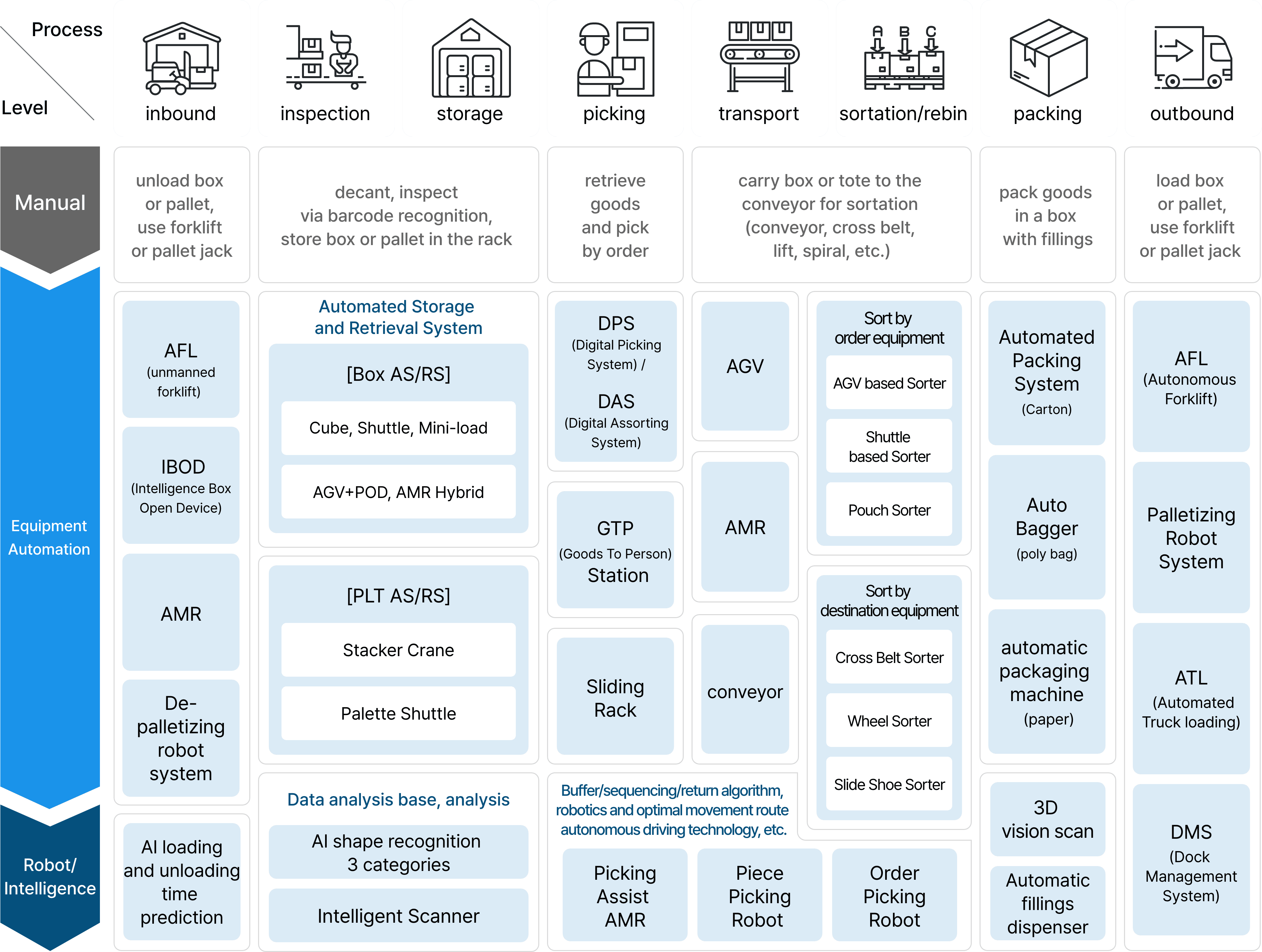
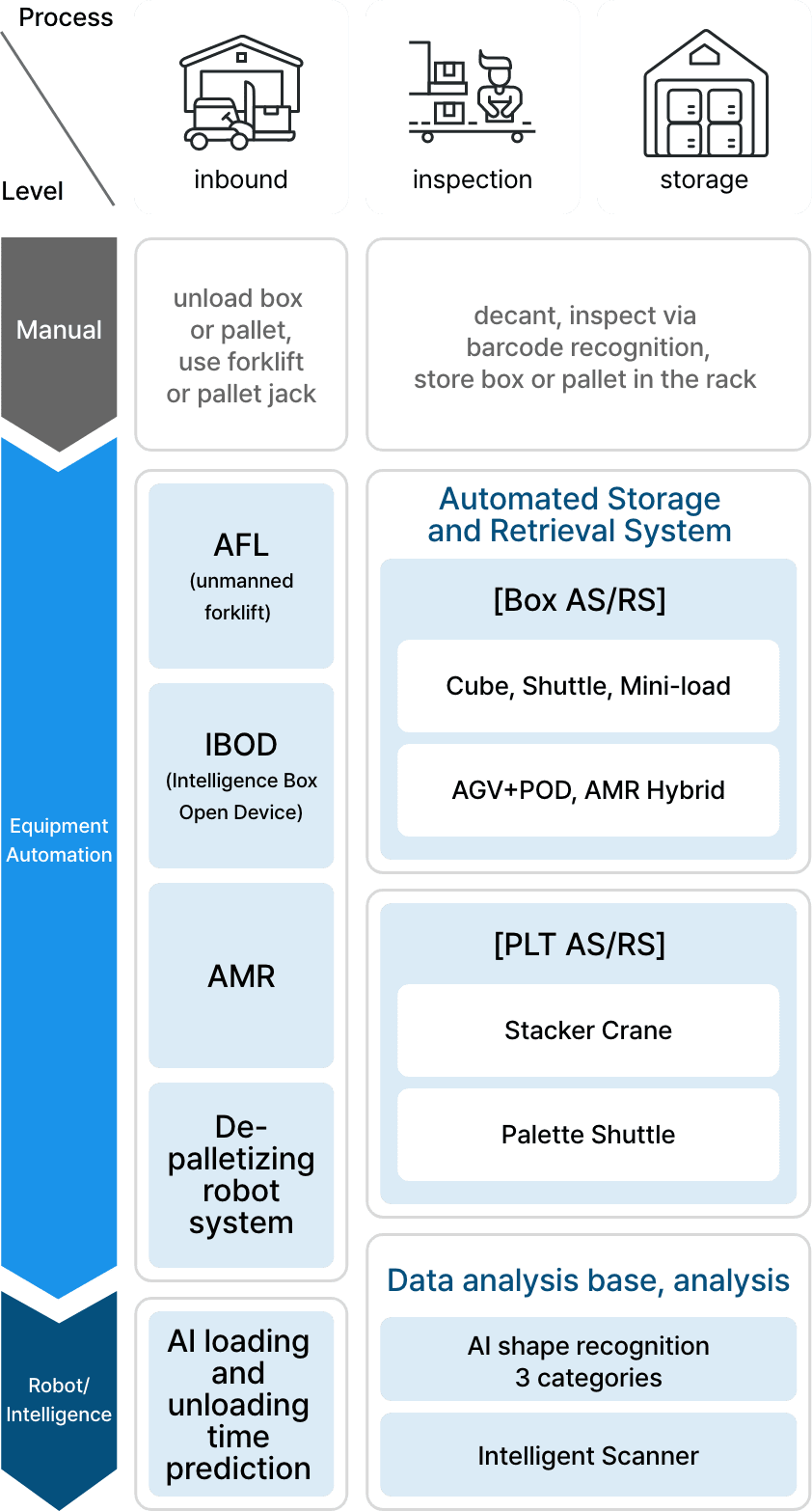
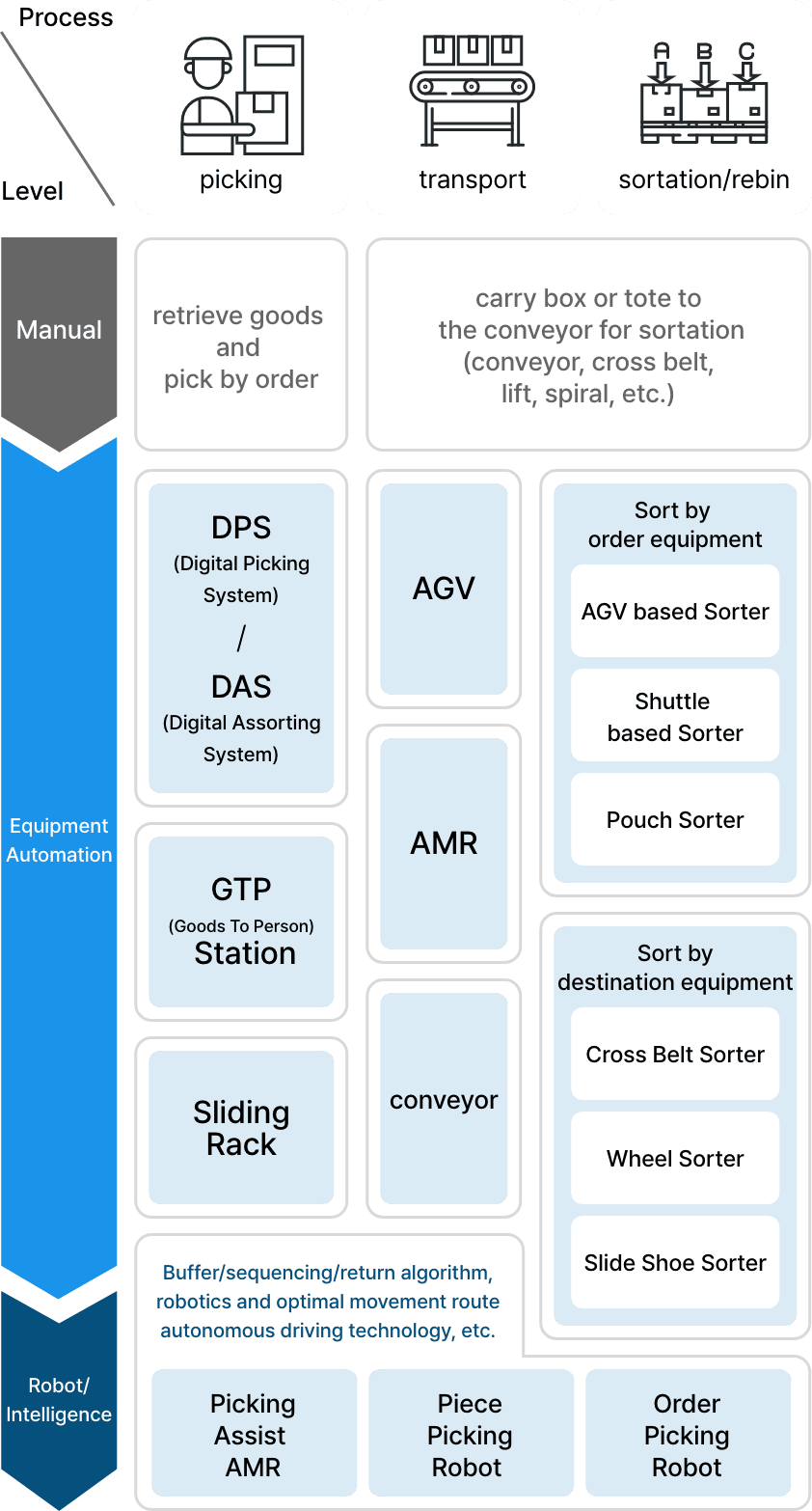
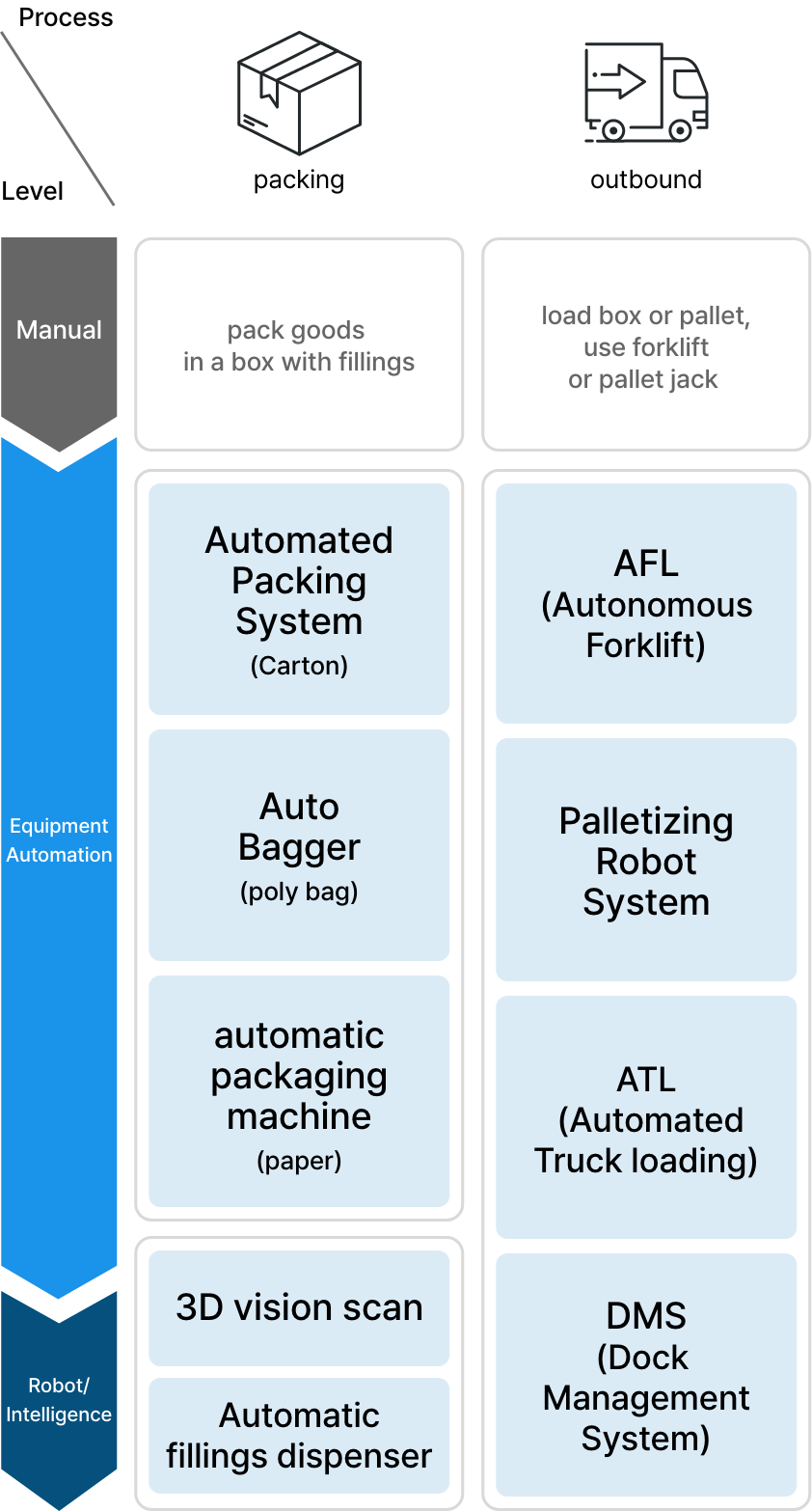
Storage and Retrieval System
Skypod
- Skypod is an AS/RS solution with AMR (autonomous mobile robot), which has autonomous picking function and moves in 3 dimensions.
- Since Skypod robot can climb up to 12m-high racks, we can overcome existing storage limitation of cube storage or moving rack solution, thus high space utilization in the warehouse.
- Any goods in the rack can be retrieved in a very short time (less than 2 minutes), and by adjusting the number of robots, the client can achieve 5 times increased throughput and scalability compared to exiting system.
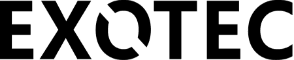
Major Projects and References (AS/RS)
- Construction of POSCO Fulfillment Center in Gwangyang Steelworks
- AS/RS based storage automation at ore lithium plants 1 and 2 of POSCO Pilbara Lithium Solution
- Phases 1 and 2 of AS/RS based storage automation at POSCO Future M cathode materials plants
- AS/RS based storage automation at POSCO’s wire rods plant
- AS/RS based storage automation at POSCO Future M smart refractory plant
Sorting System
Cross-Belt Sorter
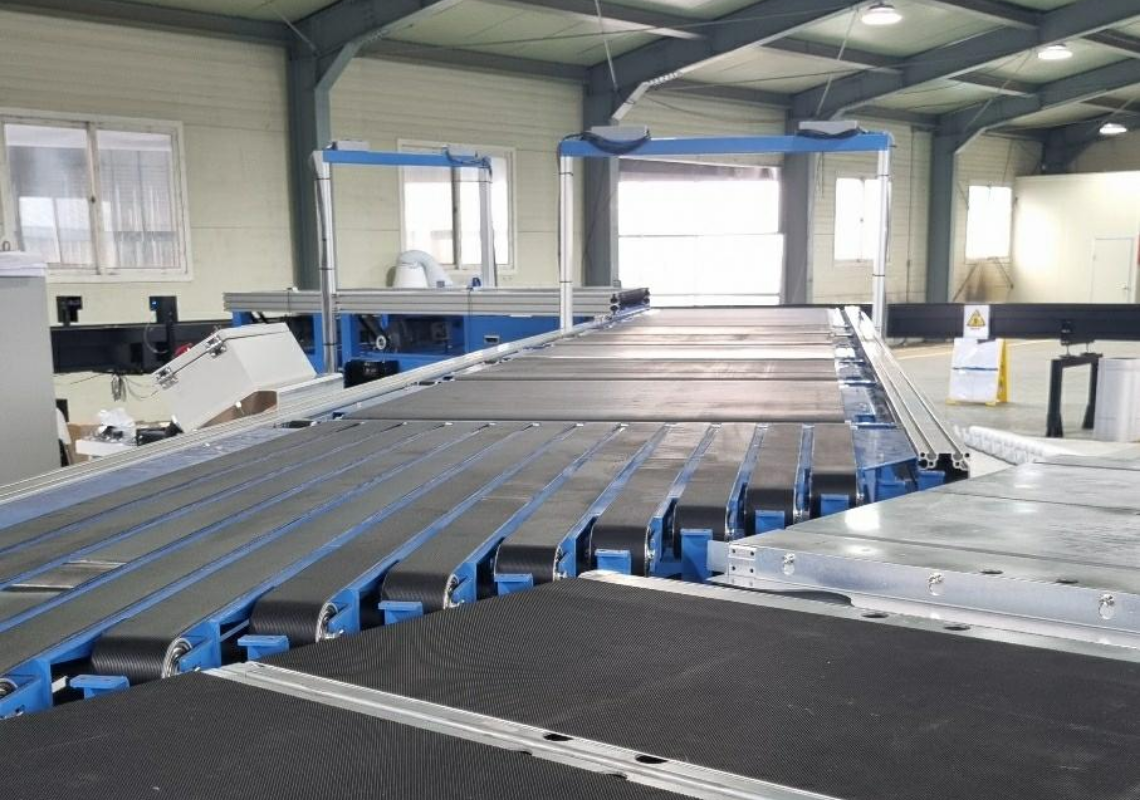
For small and medium-sized logistics centers
- POSCO DX's own LSM-type high-performance cross-belt sorter can dramatically improve product sorting throughput.
- It can handle 16,000 goods per hour at a speed of
2.7 m/s. - A flexible and efficient sorter system that uses either
1 belt or 2 belts, according to goods size. - Since the power supply to carrier adopts the non-contact method, the customer can improve durability and reduce maintenance costs.
- LSM type drive system helps to save energy and minimize noise.
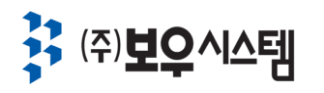
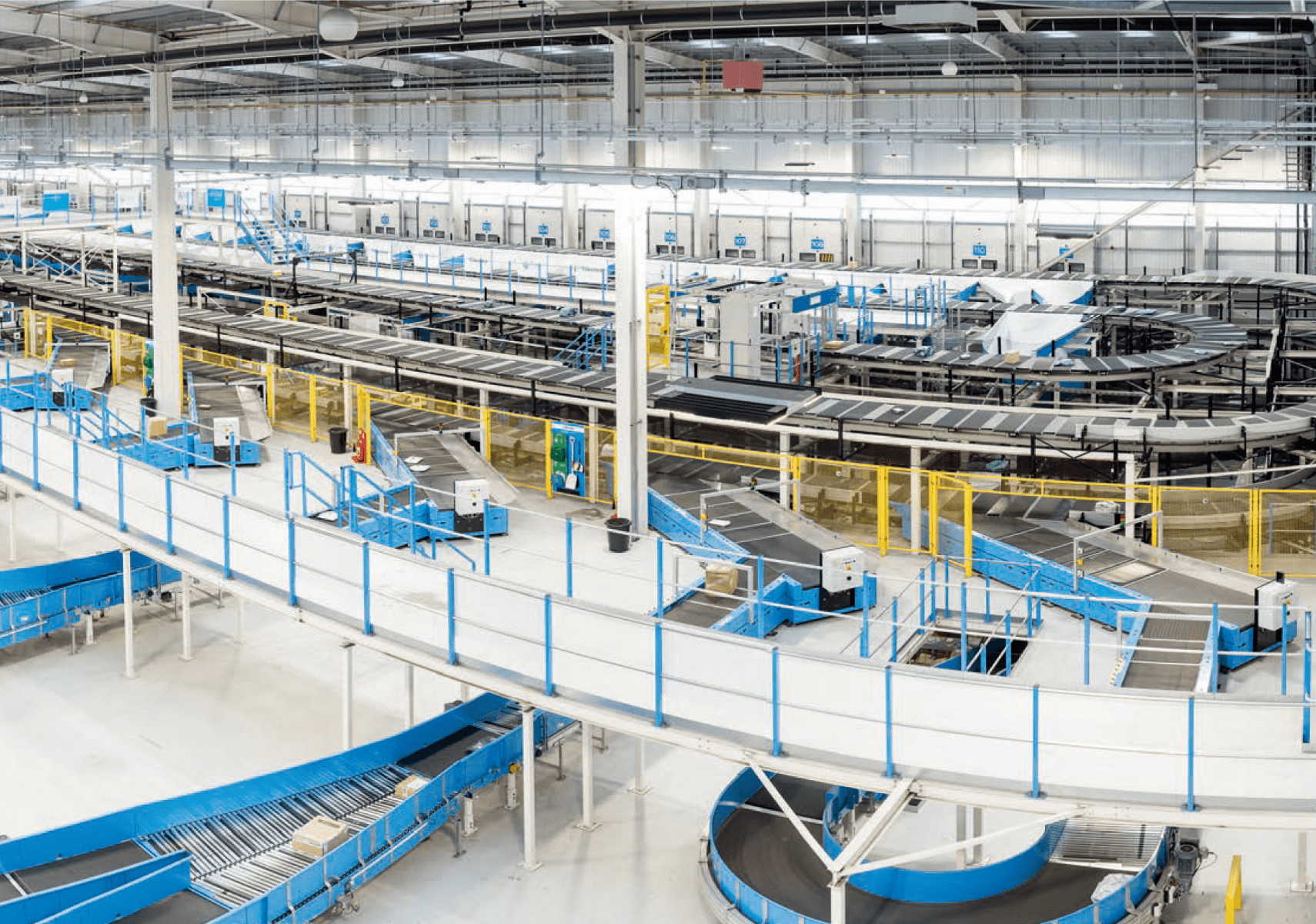
For large logistics center
- Modular type design allows for easy assembly and installation.
- It can handle up to 25,000 goods per hour at a speed of up to 3.0m/sec.
- It can handle big size goods up to 1600mm(L)*1000mm(W).
- A various type/size of carriers can be flexibly applied to quickly respond to customer needs.
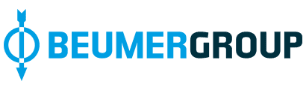
Major Projects and References (Sorter)
- Logistics automation at Hanjin Smart Mega Hub Terminal in Daejeon
- Construction and technical support at Incheon International Airport BHS project
- Logistics automation at GS Retail Gunpo new logistics center
- Logistics automation at Korea Post’s Incheon, Jeonju, and Jeju Mail Centers
Transportation System
LMR (Latent Mobile Robot)
- LMR carries mobile rack or pallets to the picking station using lifting mechanism.
- It is equipped with optimized motion performance and improved safety protection features.
- It is a productive and cost-effective solution with the superior load capacity (up to 1,500kg), CE certification, online power management, all-round safety protection, and wireless communication features.
Partnering withㅣ
Major Projects and References (AGV, RGV, Conveyor)
- Construction of POSCO Fulfillment Center in Gwangyang Steelworks
- AS/RS based storage automation at ore lithium plants 1 and 2 of POSCO Pilbara Lithium Solution
- Phases 1 and 2 of Production and AS/RS based storage automation at POSCO Future M cathode materials plants
- AS/RS based storage automation at POSCO Future M smart refractory plant
- Robot and AGV-based process automation at POSCO Future M refractory calcination plants
- AGV-based transportation automation at POSCO's electrical steel plates plant
- Logistics automation at Hanjin Smart Mega Hub Terminal in Daejeon
- Construction and technical support at Incheon International Airport BHS project
- Logistics automation at GS Retail Gunpo new logistics center
- Construction and expansion of BHS at Jeju International Airport
- Improvement of aging AVG at POSCO’s cold rolled steel plant 1
- Improvement of aging AVG at POSCO’s STS plant 1
- Logistics automation at Korea Post’s Incheon, Jeonju, and Jeju Mail Centers
LMR (Latent Mobile Robot)
- LMR carries mobile rack or pallets to the picking station using lifting mechanism.
- It is equipped with optimized motion performance and improved safety protection features.
- It is a productive and cost-effective solution with the superior load capacity (up to 1,500kg), CE certification, online power management, all-round safety protection, and wireless communication features.

- Construction of POSCO Fulfillment Center in Gwangyang Steelworks
- AS/RS based storage automation at ore lithium plants 1 and 2 of POSCO Pilbara Lithium Solution
- Phases 1 and 2 of Production and AS/RS based storage automation at POSCO Future M cathode materials plants
- AS/RS based storage automation at POSCO Future M smart refractory plant
- Robot and AGV-based process automation at POSCO Future M refractory calcination plants
- AGV-based transportation automation at POSCO's electrical steel plates plant
- Logistics automation at Hanjin Smart Mega Hub Terminal in Daejeon
- Construction and technical support at Incheon International Airport BHS project
- Logistics automation at GS Retail Gunpo new logistics center
- Construction and expansion of BHS at Jeju International Airport
- Improvement of aging AVG at POSCO’s cold rolled steel plant 1
- Improvement of aging AVG at POSCO’s STS plant 1
- Logistics automation at Korea Post’s Incheon, Jeonju, and Jeju Mail Centers
Logistics IT Solutions
We are leading the logistics automation and intelligence market by building smart logistics centers with an optimal combination of IT and equipment.
WMS (Warehouse Management System)
- WMS is a backbone system that manages all work activities in the warehouse and supports standardization and simplification of warehouse operation processes, mutual synchronization of tasks, and visualization of information.
- This system improves space utilization, shortens picking trips, and enables physical inventory and book inventory match.
WCS (Warehouse Control System)
- WCS is a system that standardizes facility control and enables real-time monitoring and precise control for advanced integration between facilities in the logistics center and smooth connection with IT systems.
- SmartPOP: POSCO DX’s own WCS solution which is capable of facility control and IT service provision.
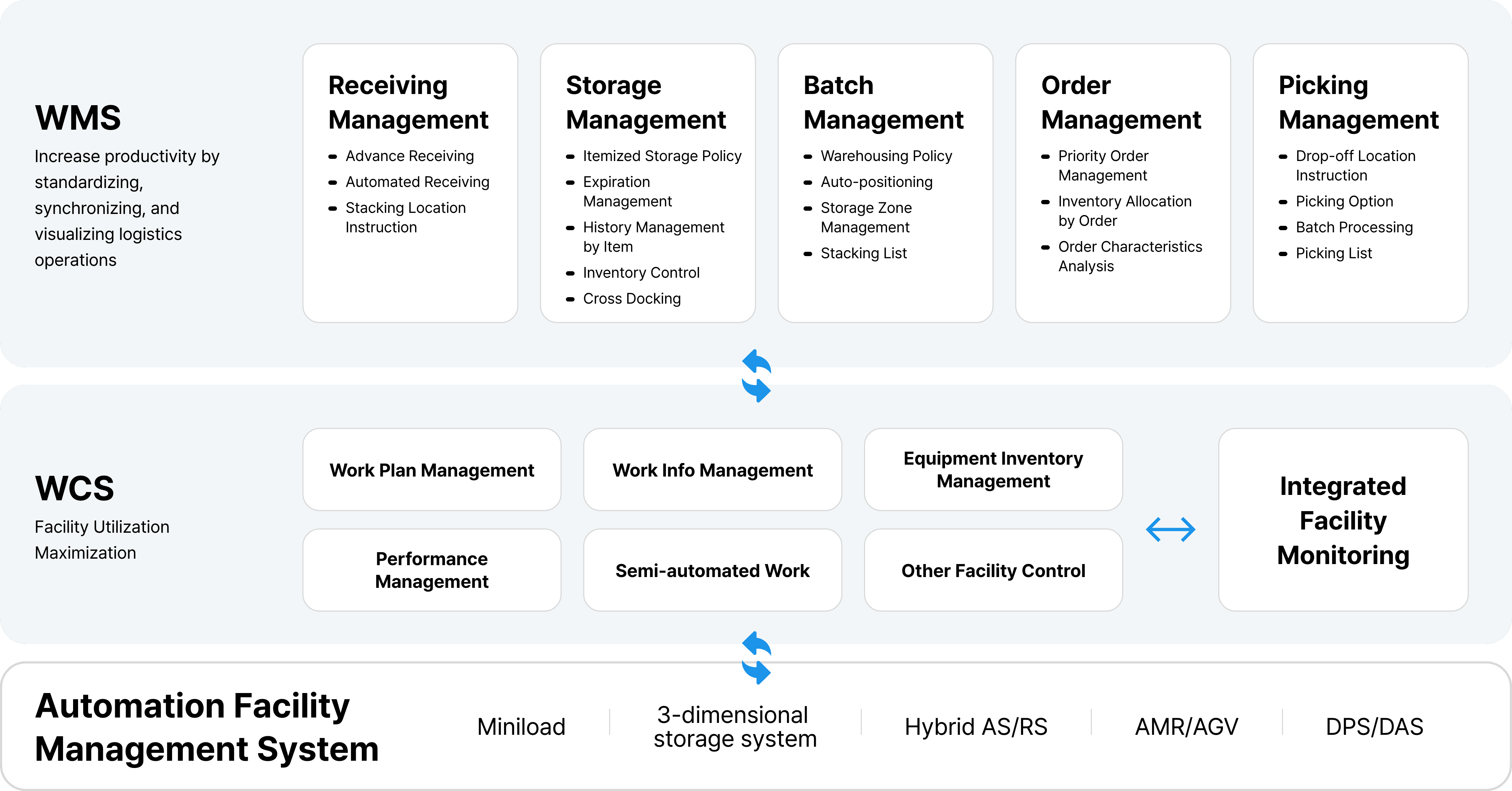

Solutions Powered by Vision AI Technology
-
AI Shape Recognition (3 Categories)
Increases worker productivity with small/medium/large classifications based on volume and automatic shape recognition for atypical shipments such as styrofoam and gunnysacks.
-
Ai-based Loading/Unloading Time Prediction
Increases accuracy by calculating progress through a combination of two depth estimation techniques (mono vision-based, top-view conversion) with a depth estimate.
DMS(Dock Management System)
DMS is a solution for controlling the movement of courier trucks operating between logistics centers (SUB↔HUB↔SUB) and monitoring the progress of work in the logistics center in real time.
TMS(Transportation Management System)
TMS is a system that directly allocates trucks to carry out logistics activities after a transportation plan is established based on customer order information and manages the scheduling and delivery process in an integrated manner.
- Opportunities to reduce transportation costs: Monitors total miles traveled by the entire fleet, number of dealership visits, etc.
- Carrying capacity improvement: Plans the vehicle allocation process with load simulation according to the material flow.
BHIMS(Baggage Handling Information Management System)
BHIMS is a platform-based, packaged solution that integrates core technologies to provide optimal customized service to baggage handling system.
It provides integrated management functions such as real-time equipment control, operation monitoring, operation information inquiry, system management, and reports.
-
Key Features of BHIMS
- Interface with Airport internal/external systems
- Find an alternate route in the event of a primary route failure
- Redundancy configuration for IT hardware, servers, and software
Main Function
- Flight Data analysis (FDA)
-
- Receiving/saving flight plan, generation of sorter information, storage of classification information, generation of simulated operation plan
- Baggage Data handling (BDH)
-
- Baggage data processing, code table creation for SSA
- Sorting System analysis (SSA)
-
- Baggage classification, sorting information sorter transmission
- Baggage Flow management (BFM)
-
- Receiving item status information, receiving facility status (Conveyor, Scanner, X-Ray, Tray tiled)
- Process Data analysis (PDA)
-
- Receive PLC/CSC error information, send defect information to MICS
- Early Baggage Storage analysis (EBSA)
-
- Early baggage storage management, baggage overflow management
- Baggage Sorting Control (BSC)
-
- Receive current baggage information, set conveyor
- Operation Station
-
- Flight data check/change, flight plan check/change, statistics check, etc.
- Interface
-
- FIS, CUS, IICS, CSC, MES