- HOME
- Solution
- Smart Factory Platform
Smart Factory Platform
We accelerate the transformation of manufacturing sites into smart factories by providing PosFrame, a data pipeline platform for operating plants, and PosML, an MLOps platform.
Data Service Platform_PosFrame
PosFrame is a smart platform that collects structured/unstructured data from production sites in real time and optimally controls them using data-based analysis and AI. PosFrame is the world's first and most advanced platform for heavy and continuous processes and can be provided on a cloud basis.
- APP
-
-
Production
-
Quality
-
Equipment
-
Energy
-
Safety
-
- PosFrame
-
5. Utilization
Portal / App Store
4. Analysis
MLOps (PosML)
3. Storage
Big Data Platform (BDP)
2. Sorting
Real Time Platform (RTP)
1. Acquisition
Interface Middleware (IFM)
6. Control
PosFame Edge
- Devices
-
Equipment
Sensor
PLC/DCS CMC
Features
-
Supports a real-time data-based decision-making system
Supports data-based decision making through real-time acquisition, analysis, and control of data generated by various IoT sensors.
-
New smart factory IT technology All-In-One platform
The real-time, fault-tolerant, integrated smart factory platform based on new technologies such as loT, Big Data, and AI continually applying new future IT technologies.
-
Successful application to continuous processes and expansion to all industries
In continuous processes, large data generated by unit facilities/processes can be analyzed horizontally and vertically to enable tracking and analysis, and management between processes.
It can be applied to all industry areas, including production acceleration, quality assurance, facility efficiency improvement, energy optimization, and proactive safety control.
Functions
-
1. Data acquisition
- Interface Middleware
-
High-speed acquisition of formatted/unformatted data from different types of systems and equipment
- Interface to multiple types of equipment
- Acquisition of large-capacity formatted/unformatted data
- Supporting data standard conversion and acquisition automation
- Real-time, high-speed acquisition (20ms-1s)
-
2. Data Sorting
- Real Time Platform (RTP)
-
Providing data life cycle management and cataloging for visualization and analysis of collected data
Provide catalogs through data standards and classifications according to customer business utilization requirements
- Create identification and standardization classification catalogs based on data governance
- Sort, reclassify, and update according to data life cycle management criteria
Provide data search engines for data visualization and analysis utilization
- Support for searches based on user demand domain classification system
-
3. Data Storage
- Big Data Platform (BDP)
-
Provides Big Data storage and analysis data pipeline
Peta Byte-level large-capacity, high-performance Big Data storage
- Compression and data duplication, cluster-based non-stop scale-out
Low-cost, high-efficiency storage of large-capacity structured/unstructured data
- Real-time high-speed processing support with Row/Column Store storage
- Object Storage-based large-capacity structured/unstructured data storage
-
4. Analysis
- MLOps (PosML)
-
This is an MLOps solution that allows even non-analysis experts to easily handle the analysis process in one stop, thereby improving the field and turning it into a knowledge asset.
-
5. Utilization
- Portal /App
-
Smart Factory Portal environment for linking data sources and data analysis utilization apps
- User-defined based Smart Factory portal dashboard
- Support for user-defined data visualization, analysis model performance monitoring
- Support system for data search, life cycle management, etc.
-
6. Control
- PosFrame Edge
-
PosFrame Edge is a solution that can artificially control equipment without speed delay by executing real-time data processing and Al. big data model near the field equipment.
Real-time data collection
- Connection to the related system following data collection from instruments, PLC/DCS, and DAQ and data preprocessing (calculation and filtering).
Smart PLC function
- Equipment sequence and process control using the software PLC function.
Real-time model control based on reinforcement learning
-
Supports the model optimization environment through reinforced learning using real-time Al and big data control model execution and control results.
*Al and big data model development and performance management use the PosFrame platform.
-
Supports the model optimization environment through reinforced learning using real-time Al and big data control model execution and control results.
Additional PosFrame features
Smart Factory Portal
The portal includes the app store providing smart apps that the user can download as needed and the 3D factory layout that provides personalized indicators, chart, and dashboard for the user to check the production status at a glance in real time.
-
3D View
The function visualizes the diffusion of the smart factory by laying out the data needed for steel mills in three dimensions.
Drill down on the smart factory by linking indicators and tasks for each factory. -
Smart App Store
Download, installation, and deployment of needed smart apps. Personalized categorization using the My Folder function.
-
Dashboard
Manage your own dashboard by selecting and placing metrics you need (specify batch charts and layouts).
Use Cases
-
- Production
- Lead-time reduction
- Pohang Iron and Steel Company's plate number marking number (painting) recognition
- POSRO shipping inspection station Wire rod product label recognition
- LS MnM (formerly LS Nikko Copper) Onsan Plant Smart Factory
- Poongsan Ulsan Plant, SNNC, POSCO Mobility Solutions Smart Factory
-
- Quality
- Securing quality in advance
- Gwangyang Steelworks Steelmaking Furnace Dart Input Status Recognition
- Reproduction of poor quality situation and analysis of root cause
- Post-process control/operation guide through slab surface quality prediction
- Quality prediction modeling through correlation analysis of quality influence factors
-
- Equipment
- Improvement of equipment efficiency
- Gwangyang Steelworks Plating Scrap Box Status Measurement
- Gwangyang Steelworks Steelmaking Steel Crane Hook Fastening Status Recognition
- Gwangyang Steelworks Hot Rolling Branch Table Coil No. and Path Recognition
-
- Safety
- Proactive safety control
- Gwangyang Steelworks Steelmaking Electrical Room, Sub-materials Risk Area Intrusion Detection (Entrance)
- Pohang Steelworks Steelmaking Main Electrical Room, Underground Culvert and Cable Cellar Inspection
- Gwangyang Coke Oven Door Gas Leak Automatic Detection
MLOps Platform_PosML
This is a solution that supports general engineers, not just IT departments, to easily and quickly implement the entire analysis process from data extraction, preprocessing, exploratory analysis and modeling, model operation, and operational management in one stop.
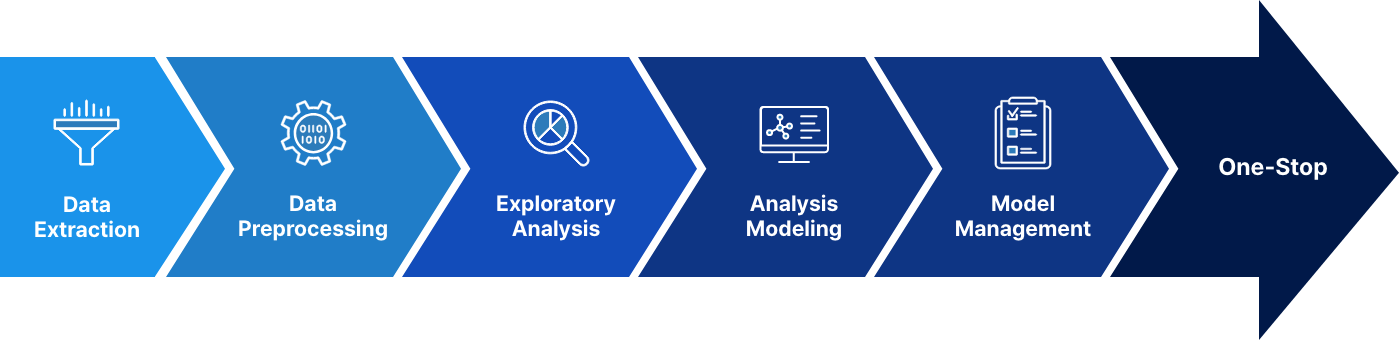
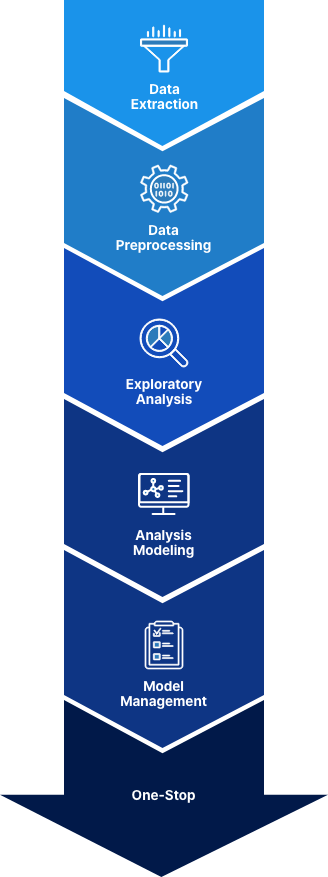
- Data Extraction
- Data Preprocessing
- Exploratory Analysis
- Analysis Modeling
- Model Management
- One-Stop
Digital Transformation’s success is determined by the level of data utilization
Manufacturing companies are collecting and storing more data due to the 4th industrial revolution, advancements in IoT, big data, AI technologies, and falling storage prices. However, many companies are unable to fully utilize the stored data due to a lack of specialized personnel and knowledge.
Features of PosML
MLOps platform that accelerates AI transformation in manufacturing sites Analysis task planning
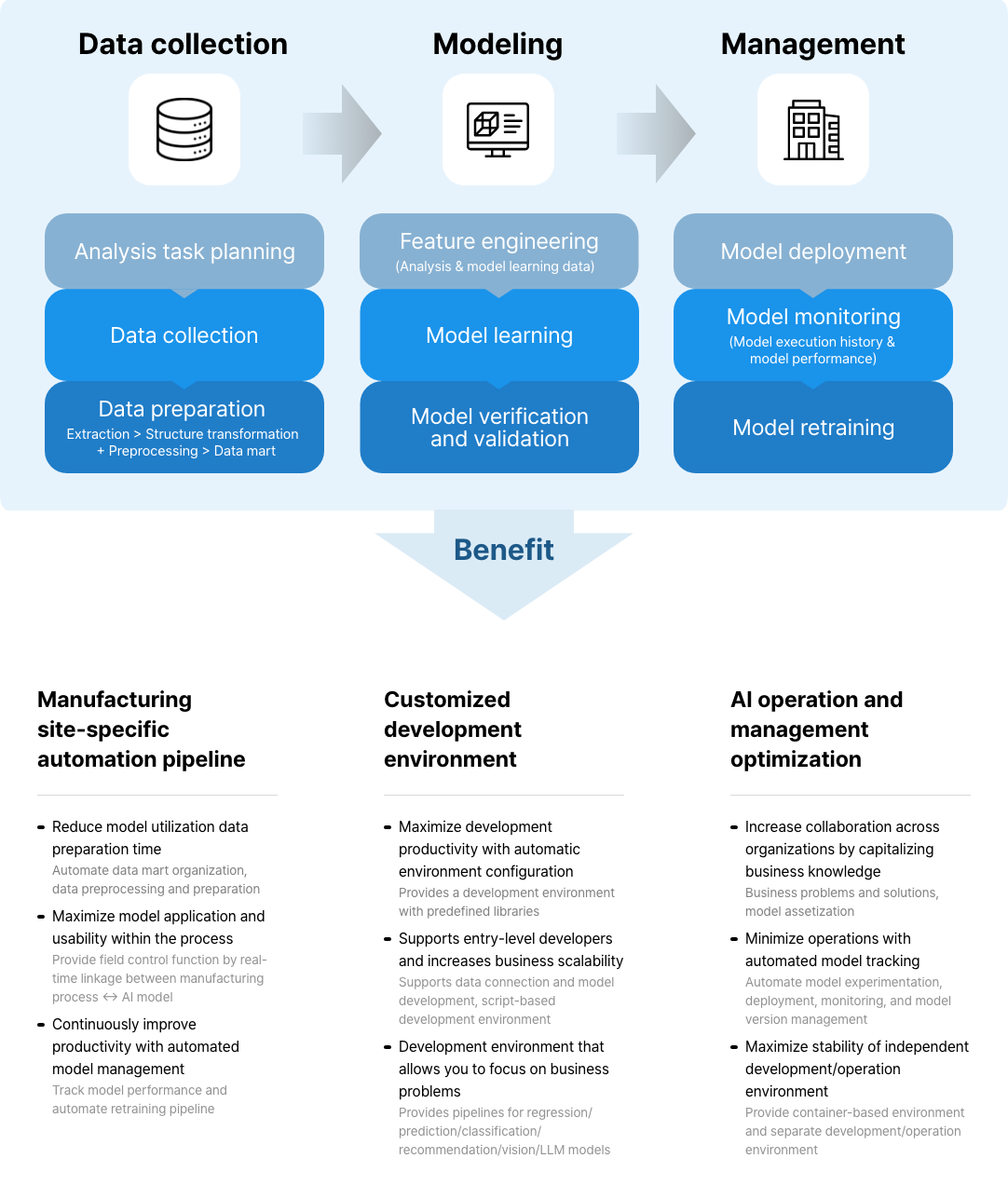

-
데이터
- 분석과정 기획
- 데이터 수집
- 데이터 준비 (추출 > 구조변환 + 전처리 > 데이터 마트)
-
모델링
- Feature Engineering (분석 & 모델 학습 데이터)
- 모델 학습
- 모델 검증 및 확인
-
운영
- 모델 배포
- 모델 모니터링 (모델 실행 이력 & 모델 성능)
- 모델 재학습
- Benefit
-
제조 현장 특화 자동화 파이프 라인
- 모델 활용 데이터 준비 시간 단축 데이터 마트 편성, 데이터 전처리 및 준비 자동화
- 공정 내 모델 적용 및 활용성 극대화 제조 공정 ↔ AI 모델 실시간 연계한 현장 제어 기능 제공
- 자동화된 모델 관리로 생산성 지속 향상 모델 성능 추적 및 재학습 파이프라인 자동화
-
사용자 맞춤 개발 환경
- 환경 자동 구성으로 개발 생산성 극대화 사전 정의된 라이브러리가 포함된 개발 환경 제공
- 초급 개발자 지원 및 업무 확장성 증대 데이터 연결 및 모델 개발 지원, 스크립트 기반 개발 환경
- 비즈니스 문제에 집중 가능한 개발 환경 회귀/예측/분류/추천/비전/LLM 모델 별 파이프라인 제공
-
AI 운영 및 관리 효율화
- 업무 지식 자산화로 조직간 협업 증대 비즈니스 문제 및 해결 방안, 모델 자산화
- 자동화된 모델 추적으로 운영 최소화 모델 실험, 배포, 모니터링 자동화 및 모델 버전 관리
- 독립적인 개발/운영 환경 안정성 최대화 컨테이너 기반 환경 제공 및 개발/운영 환경 분리
PosML Key Features
Data
Extraction
- Ability to extract data in bulk in various formats from various data sources
- · Extract data from various data sources (RDB, Hadoop, Excel, etc.) and organize it into a data mart
- · Extract data in various formats and extract large amounts of data at once, and schedule data extraction
Data Preprocessing
- After diagnosing data quality, suggest appropriate preprocessing type and automate preprocessing
- · Provides data quality diagnosis and diagnosis report based on basic statistics
- · Provides various data preprocessing functions (data type recognition, missing/outlier/duplicate value processing, etc.) and can be automatically applied when extracting data
Exploratory Analysis
- Provides features to support improved performance of data visualization and analysis algorithms
- · Provides data structure and variable relationship visualization charts (box plot, correlation coefficient analysis, etc.)
- · Provides convenience of external analysis tool linkage by providing data mart API
Analysis Modeling
- Provides a free development environment and enables modeling based on user templates
-
· Minimize development environment configuration and computing resource acquisition time by providing a container based custom development environment
- Provide customized environments for various model types such as prediction/deep learning/LLM and reuse existing development environments reflecting best practices
- · Provide customer customized modeling templates and provide chatbot linked code automatic generation/recommendation functions
Model Management
- Provides a retraining pipeline based on centralized model management and performance monitoring
- · Assetization of enterprise analysis know how through task-based analysis model management (basic model information, performance indicators, outputs, etc.)
- · Providing a model retraining pipeline based on performance monitoring of deployed models and execution history information
- · Automating model deployment in an independent operating environment and easy model prediction/execution result End Point Service linkage through provision of RESTful API
PosML in action
Used when specifically analyzing data-based issues related to improving the efficiency of operations, quality, and equipment or the cause of abnormal situations.
Use Case
-
1. Deriving Influence Factors and Detecting Anomalies
- Deriving quality influencing factors by product
- Deriving raw material price influencing factors
-
2. Analysis of Root Causes
- Root cause analysis of equipment abnormalities
- Root cause analysis of quality defects
- Causes of actual long term inventory occurrences
-
3. Developing Prediction Models
- Demand Forecasting Model Equipment Performance/Life Forecasting Model
- Delivery Forecasting Model Raw Material Price Forecasting
-
4. Developing Optimization Models
- Optimal distribution model
- Optimal mixing model
- Optimal control model
-
5. Developing Decision Models
- Defect judgment
- Automatic image classification